Living with Live Edge Furniture
After experimenting with a full range of finishes over five decades and personally living with them, it is by far the most durable, beautiful, and easy to maintain than any other thus far.
Jeffrey’s Live Edge Dining Tables can – and are meant to – be used and enjoyed daily. While not required, placemats and coasters certainly help maintain the pristine finish. A must is that trivets be used under any hot items, as scarring from heat cannot easily be remedied. We suggest felt pads on any pottery or other decorative items so they slide smoothly on the surface without scratching.
Maintenance entails wiping the surface with a damp cloth after use. We provide an initial amount of maintenance oil with each piece and a link to purchase more as needed, along with instructions for use.
The table prefers to live in an environment with a relative humidity of about 40% and not be exposed to extreme heat or huge moisture swings, just as any fine piece of furniture. As it is made from organic material there will be minor movement over its lifetime, nothing at all uncommon or that will interfere with its stability or appearance.
Our Process
Jeffrey continuously searches for the best, most reliable sources for rare slabs in raw form. Our mills notify us directly when particularly special slabs becomes available.
Not only are the slabs chosen for remarkable grain, but also for proper kilning. This is a critical factor and is why we work with long-standing relationships with trusted mills.
Each slab is moisture tested in our Studio. The proper drying of large rare slabs is time consuming and requires a highly speicalized skill set. Improperly dried seasoned wood is widely available at lower cost and frequently results in cracking and warping.
When we finish our Live Edge Slabs, there are many skilled hours that are committed to details that are not immediately obvious. These details ensure the longevity of our work.
Each slab is meticulously examined for cracking and defects. The rare slabs have from three to as many as fifteen hand-inlaid butterfly joints underneath. This dramatically reduces future problems with the progression of cracks.
We work with multiple glues and epoxy fills to address different issues. The organic tabletops are finished to present a smooth, fully practical surface with no open cracks or knots.
The top and bottom of each slab have the same number of rubbings with the superior, highly resistant non-VOC finish.
Bases are designed to permit seasonal movement without introducing stress on the rare slabs that could otherwise cause cracking.
In summary, we have taken every precaution to ensure that these one of a kind treasures of nature will last for countless generations and serve as the focal point for warm family gatherings.
About Jeffrey Greene
One of my mentors, Phillip Lloyd Powel, said to me early in my career “if you always do your best, you will never be bored with your work”. I took it to heart, and it’s still exciting to this day.
Building a dining table that will serve as a gathering place for families and friends for countless generations is a deep source of satisfaction for me.Jeffrey Greene has been professionally designing furniture for over forty years.
While growing up he lived with his painter/sculptor father George Greene in the art colony of Bucks County, PA. His father exposed him to the creative process as a way of life, as he encouraged the importance of developing his drawing skills.
He returned to New Hope, PA, in the 70’s where he set up a woodworking studio as an alternative life style rather than pursuing a career in Psychology, for which he had gone to graduate school and obtained a Masters degree.
Jeffrey Greene is largely self-taught in the art and technique of furniture design and construction, although he credits furniture maker George Nakashima, wood sculptor James Martin, and designer/artisan Phillip Lloyd Powell as formative influences.
Jeffrey Greene’s early work was inspired by George Nakashima and taken in his own direction. His current designs have come full circle returning to the live edge slab approach of construction. The many years of intervening design experience have come into play in structural innovations and subtle proportional accents in his new pieces. The introduction of custom designed metal elements of cast bronze and aluminum, as well as welded steel, are examples of these innovations.
His design process relies on the classical procedure of multitudes of freehand, artistic, conceptual drawings, followed by model making, technical drawings and pattern making. Numerous drawing books filled with conceptual sketches, comparative details, and high accuracy finished renderings that Jeffrey Greene has produced over the years have honed his design skills to a fine edge. The prolific examples of original design that you see on the website are the fruit of his labor.
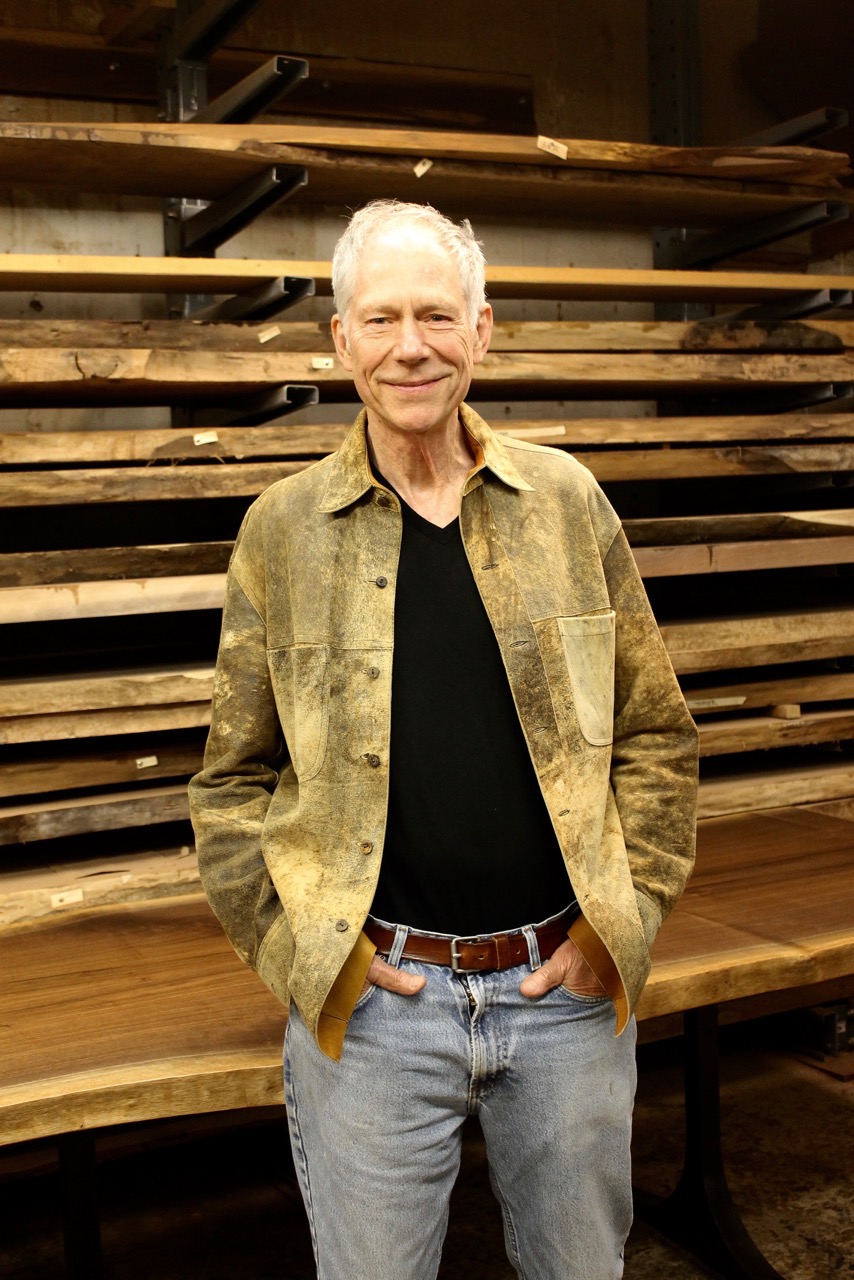